These Scientists Just Invented Wood as Strong as Steel
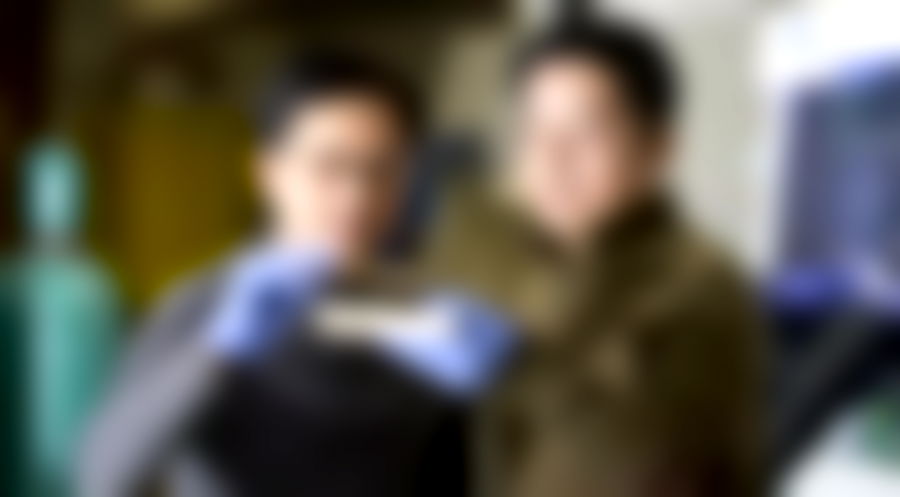

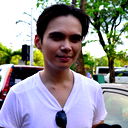
By Bryan Ke
Engineers and scientists at the University of Maryland may have just found a way to make ordinary wood as strong as steel, titanium, and even carbon fiber.
The team of engineers, led by Liangbing Hu, associate professor of materials science and engineering and a member of the Maryland Energy Innovation Institute, went into details in its journal published in Nature to explain the science behind this new process that turns normal, ordinary wood into a material that could go up against steel.
“This new way to treat wood makes it twelve times stronger than natural wood and ten times tougher,” Hu said in the journal that was released on February 8 via UMD Right Now. “This could be a competitor to steel or even titanium alloys, it is so strong and durable. It’s also comparable to carbon fiber, but much less expensive.”
Teng Li, Samuel P. Langley Professor of mechanical engineering at the University of Maryland and the co-leader of the team, explained that this new invention is not exactly that common in nature, and that it’s lighter.
“It is both strong and tough, which is a combination not usually found in nature,” he said. “It is as strong as steel, but six times lighter. It takes 10 times more energy to fracture than natural wood. It can even be bent and molded at the beginning of the process.”
During the experimentation phase, the team tried to test both the ordinary wood and the one that they invented by shooting a bullet-like projectiles through it. In the first trial, the bullet goes straight through the ordinary wood, but the second one with the fully treated wood showed promising results. The bullet did not travel the same path as in the first trial, and instead it stopped partway through.
This kind of amazing feat was done using a process that the scientists and engineers at UMD invented. According to the report, the process begins by the removal of the wood’s lignin; the part that actually makes the wood rigid and also that gives it its brown hue.
Wood then undergoes compression under mild heat at 150 Fahrenheit (65 degrees Celsius), which would cause the cellulose fibers to become very tightly packed, according to the report. Under these circumstances, scientists discovered that the fibers are so tightly packed and pressed together that they suddenly form strong hydrogen bonds.
However, this process is said to make the wood five times thinner than what it was at the beginning of the experiment.
All defects found in the wood such as holes and knots are tightly pressed together in the process. Scientists would then extend the treatment process further by coating the whole thing with paint.
“The two-step process reported in this paper achieves exceptionally high strength, much beyond what [is] reported in the literature,” Dr. Zhigang Suo, a professor of mechanics and materials at Harvard University that is not, in any way, involved in the project, said. “Given the abundance of wood, as well as other cellulose-rich plants, this paper inspires imagination.”
“The paper provides a highly promising route to the design of light weight high performance structural materials, with tremendous potential for a broad range of applications where high strength, large toughness and superior ballistic resistance are desired,” professor at Brown University, Dr. Huajian Gao, who is also not involved in the project, said. “It is particularly exciting to note that the method is versatile for various species of wood and fairly easy to implement.”
As for its usefulness, Hu explained in the journal that this wood could be used in cars, airplanes or even in buildings – or just any application where steel is typically used as its main material. More importantly, though, this is much cheaper than any of the metals mentioned.
Feature Image via University of Maryland
Share this Article
Share this Article